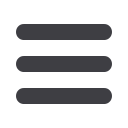
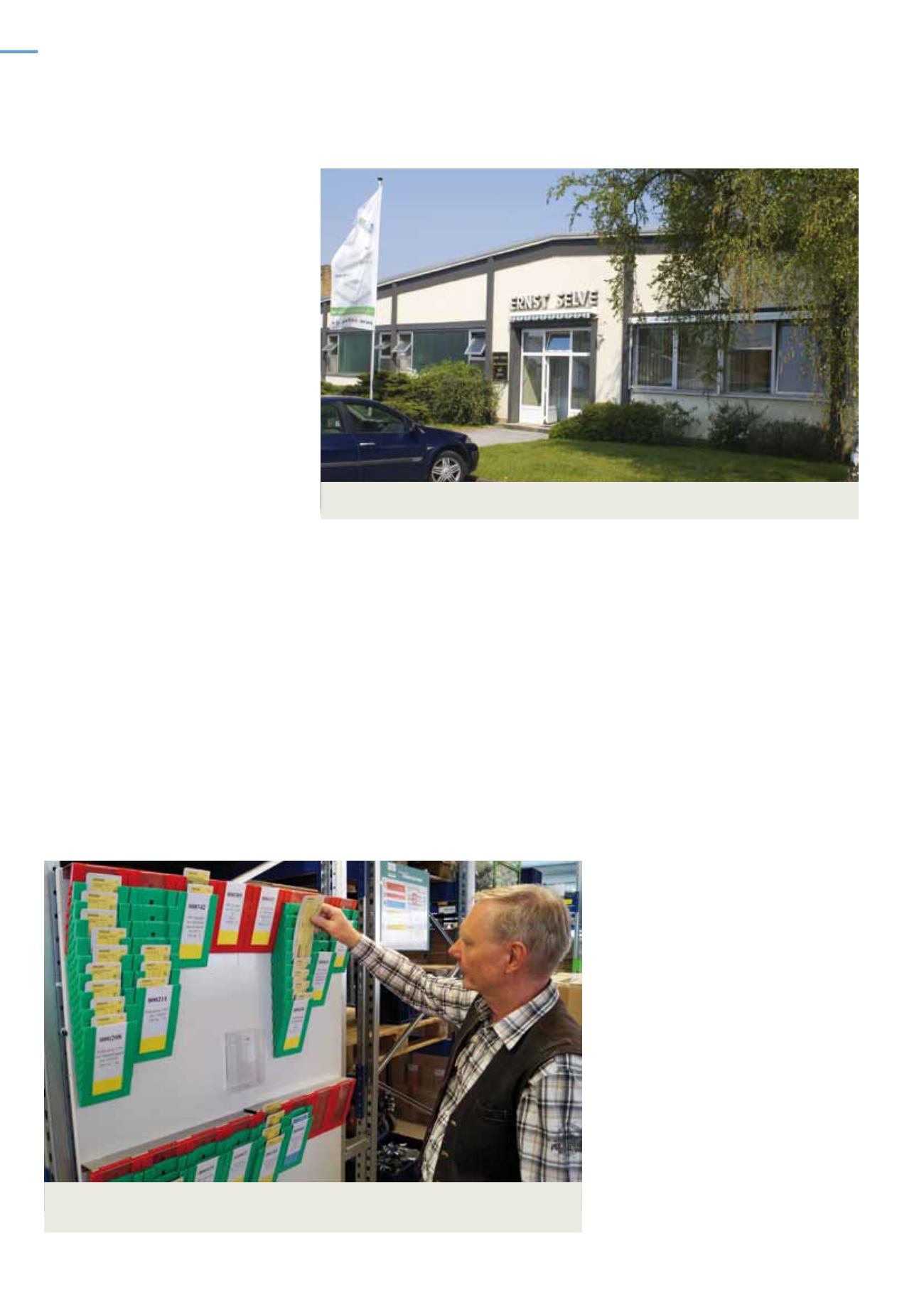
Technik
30
RTS-Magazin 7/2016
Wer bei voller Fahrt seinen Motor justiert und
dabei noch die Leistung steigert, der versteht
sein Geschäft. Gleiches gilt für Selve: Bei lau-
fender Fertigung – und für die Kunden völ-
lig unbemerkt – wurden im Zweigwerk im
hessischen Bad Arolsen nicht nur Vorgaben
der „Lean Production“ umgesetzt, sondern
auch neue Wachstumsergebnisse erzielt. Auf
rund 4,2 Millionen Gurtwickler kletterte die
Produktion in 2015. Das sind Zahlen, die
klar die Ausnahmestellung des Weltmarkt-
führers für Rollladenbauteile unterstreichen.
Und sie verdeutlichen, warum Selve zielge-
richtet auch in diesen Standort investiert.
Denn dank systematisierter Fertigung und
hochmoderner Maschinen bleibt der Wick-
ler „made in Germany“ ein Produkt mit Zu-
kunft.
Seit mittlerweile 28 Jahren ist Otto Emde
Betriebsleiter des Selve-Zweigwerks in Bad
Arolsen. Stillstand gibt es hier nicht, konti-
nuierliche Weiterentwicklungen haben seit-
her den Produktionsstandort geprägt. Ohne
hochmoderne Fertigungsautomaten läuft in
Bad Arolsen nichts. Mit ihnen werden mitt-
lerweile 80 Prozent aller Wickler produziert.
„Der hohe Automatisationsgrad macht die
Fertigung nicht nur wirtschaftlicher, son-
dern auch prozesssicherer“, betont Otto
Emde. Und so wird von Selve in den Maschi-
nenpark auch im Laufe dieses Jahres noch-
mals investiert. Ein neuer Automat für die
Fertigung der Federdosen schlägt mit rund
500 000 Euro zu Buche. Nahezu die gleiche
Summe hat das Lüdenscheider Unterneh-
men bereits in die weitere Standort- und
Zukunftssicherung seines Zweigwerks ein-
gebracht: Mit der Einführung der schlanken,
systematisierten „Lean Production“ hat sich
hier etliches verändert – zeitgleich wurde zu-
dem die Fertigungshalle erheblich renoviert.
„Lean“ als Erfolgsfaktor
„Lean spielt in ganz viele Bereiche mit hi-
nein und sorgt für entscheidende Vorteile“,
sagt Otto Emde. Im Zuge des jetzt umge-
setzten „Mammutprojektes“ wurde mit er-
heblichem internem Aufwand die gesamte
Fertigung nach Lean-Gesichtspunkten neu
strukturiert. „Das war eine große Heraus-
forderung, die wir in gemeinsamer Projekt
arbeit mit Unterstützung aus Lüdenscheid
in den vergangenen zwei Jahren gemeistert
haben“, resümiert der Betriebsleiter. So wur-
den Arbeitsprozesse effizienter gestaltet und
auch die Lagerhaltung nachhaltig optimiert.
Am Selve-Standort in der Nähe von Kas-
sel dreht sich ausschließlich alles um Gurt-
und Schnurwickler. Über 20 000 Stück wer-
den hier täglich produziert: Allen voran als
Verkaufsrenner die Mini-Wickler (0848 und
0846) mit oder ohne aufklappbarem Kunst-
stoffgehäuse sowie die sogenannten Neu-
bau-Wickler für die Unterputz-Montage.
Auf eine Vielfalt von 60 Wicklertypen ins-
gesamt bringt es Selve, die in gut 300 ver-
schiedene Varianten nach Kundenwünschen
ausgeliefert werden. Die benötigten Metall-
teile dafür werden direkt vor Ort gefertigt,
der Standort verfügt über eine eigene Stan-
zerei und auch einen eigenen Werkzeugbau.
Zwei- bis dreimal wöchentlich rollen zudem
die Laster aus Lüdenscheid mit am Haupt-
sitz produzierten Kunststoffteilen an.
Seit 1960 besteht das Zweigwerk in Bad
Arolsen. Besonders in den letzten Jahren
hat Komplettanbieter Selve hier zielgerich-
tet investiert und grundlegend moderni-
siert. Im heutigen Lean-Zeitalter präsentiert
sich in der 3200 Quadratmeter großen Fer-
tigungshalle alles im optimalen (Material-)
Fluss. Genau das ist die Kernidee von Lean.
Es gilt, Werte und Wertschöpfungsprozesse
ohne Verschwendung zu schaffen. Zu „Ver-
schwendung“ zählen beispielsweise über-
höhte Lagerbestände oder auch Warte- oder
Transportzeiten an den Arbeitsplätzen so-
wie Fertigungsautomaten. Dafür wurde im
Selve-Zweigwerk bei laufender Produktion
im wahrsten Wortsinn vieles bewegt: Ferti-
gungsmaschinen und Anlagen wurden teils
neu angeordnet, Arbeitsplätze neu gestaltet,
ein neues, hochmodernes Lagersystem mit
Barcode-Scannern eingeführt und auch ein
Kanban-System aller Fertigungsmaterialen
realisiert.
Gu(r)t gewickelt mit Lean Production
In dem Zweigwerk in Bad Arolsen dreht sich alles um Gurtwickler – nun nach den Vorgaben von „Lean
Production“.
Neue systematische Produktionssteuerung, mehr Transparenz: Mit „Lean“ sind für Otto Emde viele Vorteile
verknüpft. Eine wesentliche Neuerung ist auch die Einführung eines Kanbansystems für die Fertigung von
Baugruppen und Fertigprodukten.
Selve (4)