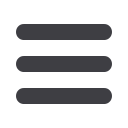
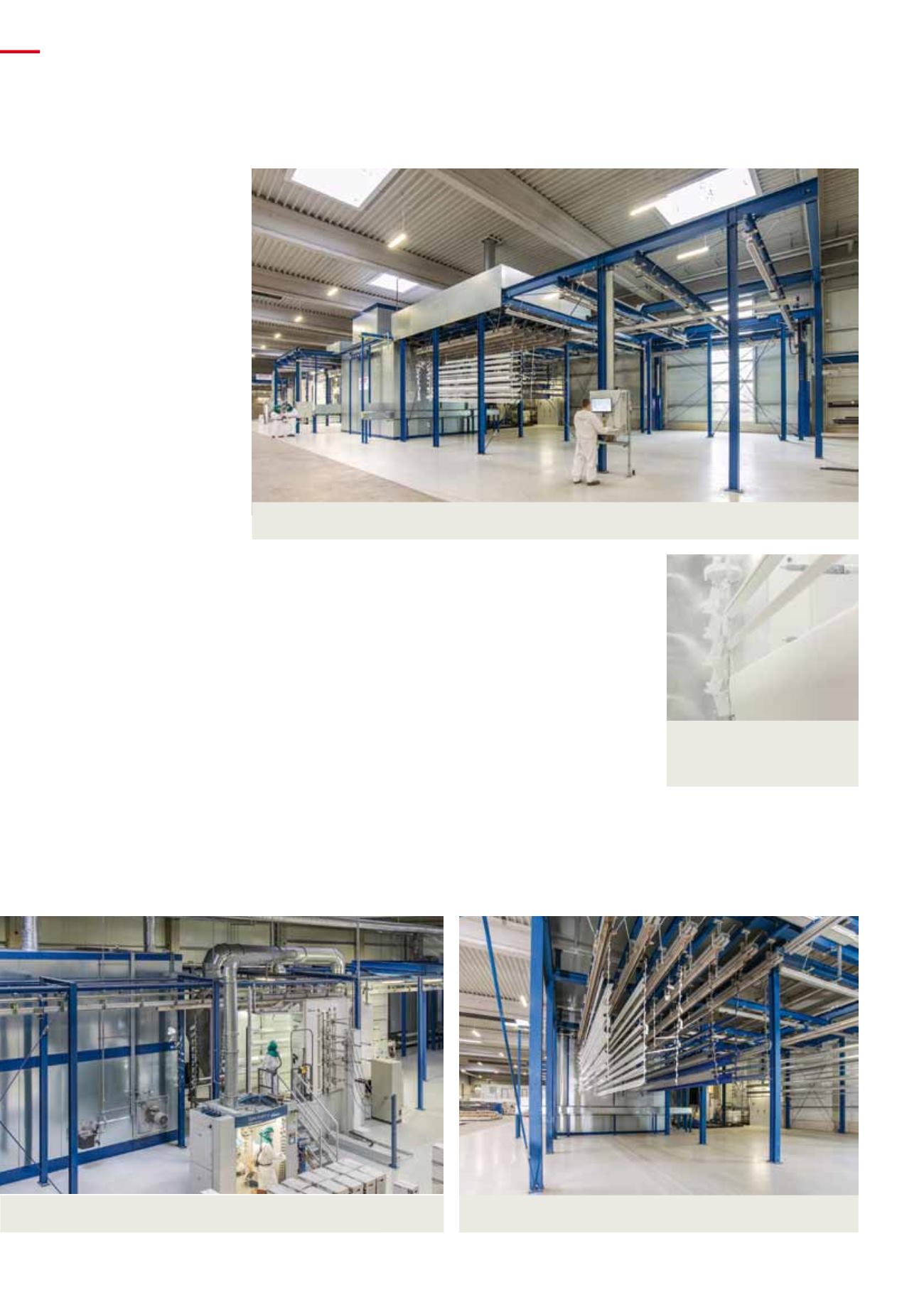
Branche
8
RTS-Magazin 7/2016
Eine eigens errichtete Produk-
tionshalle, eine neu entwickelte
Software, veränderte Produk-
tionsabläufe: Die neue Pulver-
beschichtungsanlage des Mar-
kisenherstellers
Rödelbronn
GmbH zeigt, dass mittelständi-
sche Unternehmen immer wie-
der innovative Wege einschla-
gen. Ziel ist es, eine Vielzahl von
Gestellfarben besonders flexibel
liefern zu können.
Weiß und Grau, Silber oder
gar Pink: Markisengestelle kön-
nen heutzutage nahezu jeden
Farbwunsch technisch einwand-
frei erfüllen. Allerdings: Die Lo-
gistik und der Produktionspro-
zess dahinter sind aufwendig. So
verwundert es nicht, dass Son-
dertöne oft nur mit langen War-
tezeiten und kräftigen Aufprei-
sen zu haben sind.
Die Herausforderung:
flexiblere Produktion
Markisenhersteller wie die Mön-
chengladbacher
Rödelbronn
GmbH mit ihrer Marke Varisol-
Markisen stehen daher vor der
Herausforderung, die Abläufe
rund um die Farbbeschichtung
der Gestelle zu optimieren, um
unter anderem eine hohe Viel-
falt und sehr gute Qualität zu er-
möglichen. „Bislang haben wir
unsere Markisen von einem ex-
ternen Anbieter beschichten las-
sen“, erläutert Geschäftsführer
Karl Rödelbronn. „Alleine der
Transport und die Logistik er-
Vielseitig und flexibel
fordern einen erheblichen Auf-
wand. Uns war daher klar: Wenn
wir hier einen deutlichen Fort-
schritt erzielen wollen, müssen
wir diesen Prozess direkt in un-
ser Werk integrieren.“
Große Dimensionen
Eine solche Beschichtungsan-
lage ist allerdings eine erheb-
liche Investition. Die Anlage
selbst nimmt im Falle der Rö-
delbronn GmbH eine Fläche von
1000 Quadratmetern ein, dafür
war der Bau einer neuen Halle
notwendig. Hinzu kommt ein
Schienensystem, das bis in die
benachbarte Produktionshalle
reicht. An sogenannten Shut-
tles werden die einzelnen Mar-
kisenkomponenten aufgehängt
und dann über das Schienen-
system durch die vier Stationen
der Beschichtungsanlage ge-
schleust: die chemische Vorbe-
handlung, der Trockenofen, die
eigentliche Beschichtungsstation
und der Brennofen. Ein kom-
pletter Durchlauf dauert rund
vier Stunden. Anschließend fährt
das Shuttle wieder zurück in die
Produktion, wo der Zusammen-
bau der Komponenten erfolgt.
Neue Wege
eingeschlagen
„Eine solche Anlage bietet viele
Spielräume zur Optimierung“,
so Karl Rödelbronn. „Wir haben
uns für ein sehr intelligentes Sys-
tem entschieden und sind bei der
Software sogar komplett neue
Wege gegangen.“ Ein Vorteil des
auf Schienen basierenden Shut-
Rödelbronn (8)
Der Beschichtungsprozess ist
automatisiert, schwer zugängliche
Stellen können bei Bedarf manuell
nachbearbeitet werden.
Für die neue Beschichtungsanlage hat das Unternehmen eigens eine neue Produktionshalle errichtet. Die Maschine
umfasst Komponenten zur Vorbehandlung, zur Beschichtung sowie zwei Öfen.
Die Shuttles mit den fertig beschichteten Markisenteilen: Eine neu entwickelte
Software sorgt für eine optimale Bestückung.
Die Beschichtungsanlage kann nahezu alle Farbtöne verarbeiten – im
Vordergrund sind die Kartons mit dem Farbpulver zu sehen.