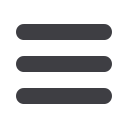
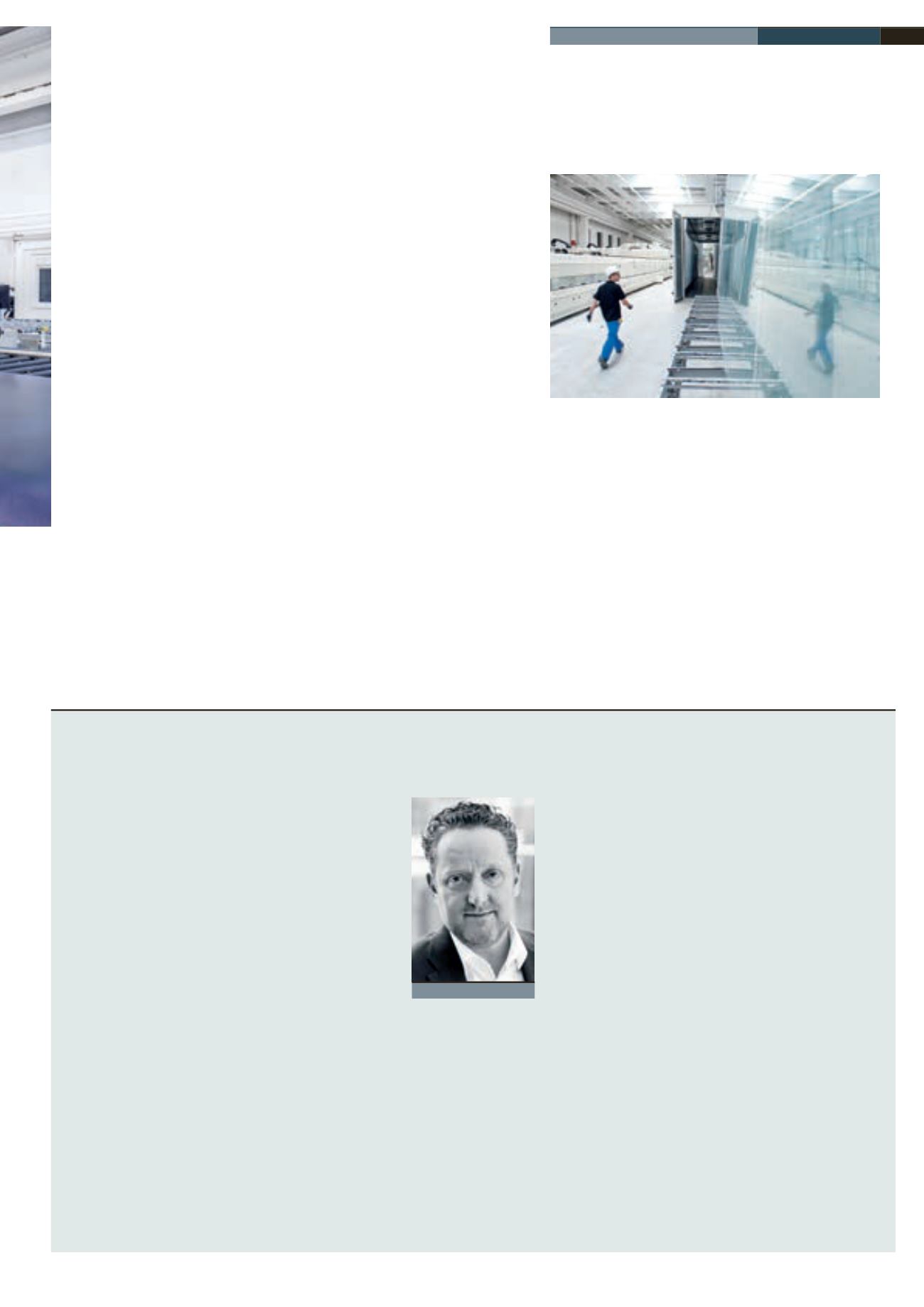
glas+rahmen
11.17
titel
17
titel
maschinen + werkzeuge
zu liefern. Die vorhandene Anlage war aber nur auf eine
Länge von 15 Meter ausgelegt. Hier lag der Grundstein
für die Anschaffung eines neuen Ofens. Darüber hin-
aus sollte die bisherige Brenntechnologie verbessert wer-
den. „Bei dieser Entwicklung floss unsere Erfahrung aus
zehn Jahren Vorspannen übergroßer Glasformate ein“,
so Theisen, „es ging darum, die Steuerung zu verbessern
und die Gesamtleistung zu erhöhen.“ Ein technischer
und letztlich auch wirtschaftlicher Meilenstein ist das
Vorspannen beschichteter Scheiben bis 16,5 Meter. Mit
einem herkömmlichen Ofen ist das nicht möglich. Der
neue Ofen von sedak ist ein sogenannter Konvektions-
ofen, mit dem sich die Wärme schnell und exakt regulie-
ren lässt. Auch die sogenannte „Quench“, in der das vor-
gespannte Glas abkühlt, erhielt einen „Technologie-Lift“
– weil beschichtete Scheiben schneller auf Luftverän-
derungen reagieren. In diesem Anlagenteil können die
Bediener nun gezielt den Herstellprozess beeinflussen.
Wissen ist nicht skalierbar
Beschichtetes Glas vorzuspannen ist nicht neu. Aller-
dings kann das Wissen und die Technologie nicht von
Standardformaten eins zu eins auf übergroße Glasfor-
mate übertragen werden. Mit jedemMeter Glas gestaltet
sich der Vorspannprozess schwieriger. „Fehler in dieser
Stufe lassen sich nicht mehr korrigieren und verschlim-
Glas+Rahmen fragte Ulrich Theisen, Prokurist und Leiter
Vertrieb bei sedak, nach den Herausforderungen bei der
Planung des 16,5-Meter-Ofens.
g+r:
Welche Gründe waren ausschlaggebend für die
Planung eines Ofens, der übergroße, beschichtete Schei-
ben vorspannen kann?
theisen:
Gläser größer als neun Meter werden immer
beliebter, daher haben wir zunächst die Lieferkapazität
erhöht. Durch die Möglichkeit, nun bereits beschichte-
te Gläser dieser Größe vorspannen zu können, haben wir
zudem unser Ziel realisiert, solche Scheiben schneller und
in konstant hoher Qualität zu produzieren.
g+r:
Wo lag die besondere Herausforderung?
theisen:
Die Anforderungen an Fassadengläser sind
hinsichtlich ihrer bauphysikalischen Eigenschaften im-
mer weiter gestiegen. Um diese zu erfüllen, sind die Be-
schichtungen immer komplexer geworden. Das gilt für
Sonnenschutz- wie für Wärmeschutzbeschichtungen.
Nun sind es gerade diese Beschichtungen, die einen emi-
nent hohen Einfluss auf das Ergebnis im Ofen haben. Es
ist eben ein Unterschied, ob eine Scheibe mit einer Drei-
mern sich im weiteren Produktionslauf “, erklärt Ulrich
Theisen. Abweichungen bei Planität oder Format wären
schnell Ausschuss. Daher lohnt es sich, hohen Aufwand
in die perfekte Produktion zu investieren, denn das Er-
gebnis überzeugt: Millimetergenau gefertigte, ultraplane
Hochleistungsgläser, die zügig zur gewünschten Funkti-
onsglaseinheit weiterverarbeitet werden – ein perfektes
Zusammenspiel von hochmodernen Anlagen und erfah-
renen Glas-Profis. „Ohne das Know-how unserer Anla-
gensteuerer wäre eine fehlerfreie Produktion nicht mög-
lich: Sie wissen, wann welche Maschineneinstellung ge-
gebenenfalls anzupassen ist“, weiß Ulrich Theisen. Auf
die Frage, mit welchen Partnern sedak den neuen Ofen
realisiert hat, hält man sich bedeckt.
www.sedak.comfach-Silber-Schicht oder mit einer Nickel-Chrom-Schicht
durch den Ofen fährt. Der Ofen muss also auf die jewei-
lige Besonderheit der Scheibe einstellbar sein – und der
Maschinenführer muss wissen, wie Scheibe und Ofen auf
den Brand reagieren. Unsere Fachleute sind im Umgang
mit der ESG-Anlage sehr erfahren. Übrigens: Bei einigen
besonderen Beschichtungen ist ein Vorspannen auch jetzt
nicht möglich. Dann erfolgt die Produktion umgekehrt –
und die Gläser erhalten ihre Funktionsschicht erst, wenn
sie durch den Ofen gegangen sind.
g+r:
Was ist neben der Größe das besondere an Ihrem
neuen Ofen?
theisen:
Der neue Ofen funktioniert nach dem Kon-
vektionsprinzip. Dadurch ist es möglich, ihn gleichmä-
ßig durchzuheizen, aber auch, einzelne Teilbereiche sehr
gezielt nachzusteuern. Das haben wir durch verbesser-
te Heizkreise gelöst, über die sich die Steuerung we-
sentlich schneller und feiner austarieren lässt. Hinzu
kommt, dass die Entwicklung in enger Abstimmung mit
dem Hersteller lief. So flossen unsere zehnjährige Erfah-
rung im Vorspannen und die Erfahrung unseres Partners
im Ofenbau ein.
GLAS+RAHMEN INTERVIEW
AUF DIE BESONDERHEITEN DER SCHEIBEN EINSTELLBAR
Zusätzlicher Qualitäts-
test für ESG-Scheiben:
sedak-Scheiben werden
im Regelfall in der
Heat-Soak-Kammer
nach dem Vorspannen
nochmals erhitzt. So
können Spontanbrüche
aufgrund von z.B. Ni-
ckel-Sulfid-Einschlüsse
verhindert werden.
Ulrich Theisen
Fotos: © sedak GmbH & Co. KG | Fotograf: René Müller
„Die Anforderungen
an Fassadengläser
sind hinsichtlich
ihrer bauphysikali-
schen Eigenschaften
immer weiter gestie-
gen.“